Understanding the Importance of Proper Clean Room Design
Clean rooms are essential environments for various industries, including pharmaceuticals, electronics, aerospace, and medical device manufacturing. These controlled spaces are designed to minimize airborne particles and maintain specific environmental conditions crucial for sensitive processes and products. The importance of proper clean room design cannot be overstated, as it directly impacts the quality, safety, and efficiency of operations within these specialized facilities.
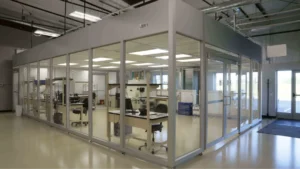
Why Strong Design Matters
A well-designed clean room is fundamental to maintaining the required level of cleanliness and environmental control. Here’s why strong design is critical:
- Contamination Control: The primary purpose of a clean room is to prevent contamination. A properly designed clean room effectively manages airflow, filtration, and pressurization to minimize the introduction and spread of particles.
- Regulatory Compliance: Many industries are subject to strict regulations regarding clean room standards. A well-designed clean room ensures compliance with these regulations, avoiding potential legal and financial consequences.
- Product Quality: In industries such as pharmaceuticals and electronics, even microscopic contaminants can compromise product quality. A robust clean room design helps maintain consistent product quality and reduces the risk of defects.
- Operational Efficiency: An efficiently designed clean room optimizes workflow, reduces the risk of contamination, and minimizes the need for rework or product rejection.
- Cost-Effectiveness: While initial investment in a well-designed clean room may be higher, it can lead to long-term cost savings through improved efficiency, reduced contamination incidents, and lower maintenance requirements.
Types of Clean Rooms
Clean rooms are classified based on their level of cleanliness and the specific requirements of the processes they house. The main types include:
- Modular Clean Rooms: These are pre-fabricated, flexible structures that can be easily assembled, modified, or relocated. They are cost-effective and offer quick installation.
- Stick-Built Clean Rooms: These are traditional clean rooms constructed on-site using conventional building materials. They offer customization but may require longer construction times.
- Softwall Clean Rooms: These use clear vinyl curtains suspended from metal frames to create walls. They are economical and easily movable, suitable for less stringent cleanliness requirements.
- Hybrid Clean Rooms: These combine modular components with existing conventional construction walls, offering a balance between flexibility and integration with existing structures.
- Pharmaceutical Clean Rooms: Specifically designed for pharmaceutical manufacturing, these rooms adhere to strict regulatory standards for air quality, material flow, and personnel management.
- Medical Device Clean Rooms: These are tailored for the production of medical devices, ensuring compliance with industry-specific regulations.
Clean Room Standards and Certification
Clean rooms are certified according to various standards, with ISO 14644-1 being the most widely recognized international standard. The ISO classification system ranges from ISO Class 1 (cleanest) to ISO Class 9 (least clean)7. Here’s a brief overview of the standards:
- ISO 14644-1: This standard defines clean room classifications based on the concentration of airborne particles. It specifies the methods for testing and monitoring clean rooms to prove compliance.
- EU GMP: The European Union Good Manufacturing Practice guidelines provide standards for pharmaceutical clean rooms, focusing on contamination control and product quality.
- FDA Regulations: In the United States, the Food and Drug Administration sets standards for clean rooms in pharmaceutical and medical device manufacturing.
- FS209E: An older U.S. federal standard that classified clean rooms from Class 1 to Class 100,000. While largely replaced by ISO 14644-1, some industries still reference this system.
The certification process typically involves:
- Planning and Preparation: Identifying specific regulations and standards to be met.
- Testing and Evaluation: Assessing air quality, temperature, humidity, and other parameters.
- Documentation: Generating a detailed report of test results and observations.
- Certification: Issuing a certificate if the clean room meets the required standards.
Materials Qualified for Clean Room Standards
The selection of materials for clean room construction and equipment is crucial to maintain the required level of cleanliness. Here are some common materials used in clean rooms:
Walls and Ceilings:
- Epoxy-coated gypsum board
- Powder-coated steel panels
- Fiberglass reinforced plastic (FRP) panels
Stainless steel panels
Flooring:
- Epoxy coatings
- Vinyl flooring with anti-static properties
- Raised access flooring systems
Furniture and Fixtures:
- Stainless steel
- Powder-coated aluminum
- High-density polyethylene (HDPE)
Filtration Systems:
- HEPA (High-Efficiency Particulate Air) filters
- ULPA (Ultra-Low Penetration Air) filters
Cleanroom Apparel:
- Non-shedding fabrics
- Polyester or polyester-cotton blends
- Specialized cleanroom garments with anti-static properties
Cleaning Supplies:
- Specialized detergents and disinfectants
- Low-particle generating cleaning tools
These materials are chosen for their ability to minimize particle generation, resist chemical degradation, and withstand frequent cleaning and sterilization processes.
Key Design Considerations
When designing a clean room, several factors must be carefully considered:
- Airflow Management: Proper airflow design is crucial for maintaining cleanliness. Unidirectional airflow systems are often used in higher-class clean rooms to minimize turbulence and efficiently remove particles.
- Filtration Systems: The selection and placement of HEPA or ULPA filters are critical for achieving the required air quality.
- Pressurization: Maintaining positive pressure within the clean room prevents the ingress of contaminants from surrounding areas.
Temperature and - Humidity Control: Precise control of these parameters is essential for many processes and can affect particle behavior.
- Material and Personnel Flow: Designing efficient workflows and implementing proper gowning procedures help minimize contamination risks.
- Lighting: Proper lighting design is important for visibility and to minimize shadows that could hide contaminants.
- Surface Finishes: Smooth, non-porous surfaces that are easy to clean and don’t generate particles are essential.
- Maintenance Access: Designing for easy maintenance of HVAC systems and other equipment without compromising cleanliness is crucial.
Conclusion
Proper clean room design is a complex but essential process that requires careful consideration of numerous factors. From selecting the right materials and equipment to implementing effective airflow and filtration systems, every aspect of the design impacts the clean room’s performance and compliance with industry standards.
For organizations seeking expertise in clean room design and construction, partnering with experienced vendors is crucial. ASA Thermacoustic stands out as a vendor of choice, particularly due to their extensive experience in HVAC systems. Their expertise in designing and implementing advanced air handling and filtration systems is invaluable for maintaining the strict environmental controls required in clean rooms.
By leveraging ASA Thermacoustic’s experience, companies can ensure that their clean room design not only meets current standards but also incorporates the latest innovations in HVAC technology. This can lead to improved energy efficiency, better contamination control, and ultimately, a more reliable and effective clean room environment.
In an era where product quality and regulatory compliance are paramount, investing in a well-designed clean room with the help of experienced partners like ASA Thermacoustic is not just a necessity—it’s a strategic advantage that can drive innovation, quality, and success in industries that depend on controlled environments.